Before the advent of state-of-the-art simulators, practicing emergency situations in the aircraft was standard procedure. It is still the procedure used in much of General Aviation and, for the most part, works well in preparing for the unexpected. However, as this month’s reports dealing with simulated engine failures show, precautions have to be taken to prevent training scenarios from leading to real mishaps. A Traveler's Shortcoming This student pilot’s use of the first-person singular (I) throughout the description of this incident in an AA-5 Traveler seems to indicate that the instructor was not inclined to intervene. This can be a good training technique, but only up to a point. In this case the point was about 100 feet short of the runway. ■ While cruising at 2,500 feet, my instructor pulled the power to idle, applied carburetor heat and told me that I had just lost engine power. I pitched for best glide and performed a flow check for a restart. I then decided to head for [a nearby airport]…. I made a radio call and entered the pattern on a 45-degree downwind at pattern altitude for Runway 28. I added 10 degrees of flaps on downwind also. I then made a radio call to turn left base for Runway 28, made the turn and added flaps to 20 degrees. I then made the radio call for final which was to be a full stop and made the turn. I added full flaps shortly after making the turn to final. It was looking like it was going to be close for making the touchdown point. On short final I decided to add some power just to be sure I was going to make the runway. At about half throttle the main wheels came in contact with the deep snow on the ground and then the nose wheel came down. The nose wheel folded over when it hit a snowmobile track which resulted in a propeller strike. I skidded to a stop about 100 feet short of the runway. The main contributing factors for not making the runway were: 1. I did not add full throttle and added throttle too late…. 2. The point of touchdown is about 15 feet higher than the approach end of the runway. With the snow, the perception of contour may have been distorted and hindered my judgment of height. "The horn, the horn, the lusty horn, Is not a thing to laugh to scorn." — William Shakespeare In the following report, a C182 pilot performed a simulated engine failure while undergoing a practical examination. It appears that both the examiner and the examinee were so engrossed in the simulated emergency that they both tuned BEEEEP out BEEEEP the BEEEEP gear BEEEEP warning BEEEEP horn. ■ At roughly 1,900 feet over [the airport], a simulated engine failure was initiated by the Examiner. I immediately pulled the carburetor heat on, pitched for best glide and started a right turn to land on Runway 36. While circling to land, I went through the engine troubleshooting procedures and made a simulated emergency call over the CTAF (Common Traffic Advisory Frequency). At this point we were on final. The aircraft was high, so I put in full flaps and initiated a forward slip to dissipate altitude. The aircraft landed long with the gear up. As soon as I realized that the gear was not down, I secured the engine (mixture— idle cutoff, fuel selector— off, master— off, ignition switch— off). At no point during the maneuver did I hear any indication from the Examiner that the gear was not down or that I should initiate a go around. I believe that causal factors in this incident were nervousness and stress associated with the practical examination as well as a poorly executed power-off approach resulting in distraction on final. A number of actions on my part could have prevented this incident. The most obvious and sure method of prevention would have been to put the gear down immediately after the simulated engine failure. This would have solved the problem at its root. Additionally, during the course of the maneuver, a number of factors led to my inability to recognize that the gear was not down. I failed to complete a GUMP check (Gas on fullest tank, Undercarriage [gear] down, Mixture full rich, Prop full forward) on final. Additionally, better execution of the power-off approach would have allowed adequate time and altitude to utilize the checklist. Since we were high on final, my concentration was on getting the aircraft down (using full flaps and a forward slip) rather than verifying that the aircraft was configured for landing. Additionally, it is my opinion that nerves and stress associated with the practical examination led to my inability to recognize the gear warning horn. Finally, I should have initiated a go-around maneuver as soon as I realized that we were going to land long. Keeping It Unreal When faced with a real engine failure, performing the Engine Secure Checklist reduces the chance of a fire on landing. However, actually performing the steps in the Engine Secure Checklist when the engine failure is not real can lead to a real problem. ■ While I was instructing a student in simulated forced landings, the student went through an Engine Secure Checklist. At some point during the descent, the student turned off the fuel selector without verbalizing his actions. Because the aircraft has a fuel selector handle that points in opposite directions in the ON and OFF positions, I mistakenly thought the fuel selector handle was in the ON position. At approximately 500 feet AGL, the go-around was initiated and the engine quit. I took control and successfully made a forced landing on a dirt road without incident. This could have been prevented by ensuring that students only verbalize the secure flow check and do not actually move the fuel selector, mixture and magnetos to off. Bogged Down Activating carburetor heat and periodically clearing the engine are two procedures that should be used when simulating an engine failure in a light aircraft. The instructor who submitted this report failed to use either procedure and ended up in a sticky situation. ■ I was conducting a VFR training flight. At 6,000 feet MSL, I gave the student a simulated engine failure. At approximately 200 feet over an open field, with the landing assured, I asked the student to recover the aircraft. Upon applying full power, the engine began sputtering and ran very rough and was not developing full power. I announced that I had control of the aircraft, verified full throttle and placed the carburetor heat on. At this point the aircraft had descended through 50 feet AGL and was still sputtering and developing 50 percent power at best. It was apparent that the aircraft was going to touch down. I performed a soft field landing, but the aircraft immediately bogged down on the soft mud and came to a stop. I secured the aircraft and called for assistance on my cell phone. Even though I was communicating with ATC, it was my judgment that there was no need to declare an emergency. In order to prevent a recurrence of this situation, I will ensure that carburetor heat is on and occasionally clear the engine by momentarily increasing the RPM during the simulated engine out, best glide portion of the procedure. Another One Bites the... Mud Even when carburetor heat is used and the engine is cleared, it is still possible to wind up in the mud if recovery from a simulated engine failure is initiated too late. 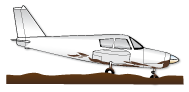 ■ I was practicing an emergency engine out procedure. I pulled the throttle to idle to simulate a lost engine, maintained flight attitude for best glide, put the carburetor heat on, mixture rich, fuel pump on and switched the fuel tanks. I then started looking for a field to aim for. I periodically cleared the engine and continued with my procedures, checked the primer and simulated restarting the engine. Heading toward the field, I entered on a left downwind setting myself up to land northward. I simulated transmitting a Mayday call of my situation and position. I turned final with full flaps. I kept gliding down to ensure that I would make the field if indeed my engine had failed. By the time I applied full power to go around, I was too low and the mains touched the ground. I had no intention of touching down. My altitude judgment was in error. The ground was very soft and muddy and I could feel the mud grabbing hold of the tires and slowing the aircraft down. I pulled the yoke full back and kept in full power in an attempt to get back off, but it was no use. The mud kept slowing the aircraft down and forced the nose down. When the nose gear hit, it buried itself in the mud along with half the prop blade, bringing the aircraft to a full stop. Luckily the plane had slowed up enough before the nose gear hit. If I were going any faster, the aircraft would have flipped over. | CALLBACK Issue 383 ASRS Online Resources October 2011 Report Intake: | Air Carrier/Air Taxi Pilots | 2,787 | General Aviation Pilots | 965 | Controllers | 639 | Cabin | 348 | Mechanics | 155 | Dispatcher | 39 | Military/Other | 12 | TOTAL | 4,945 | ASRS Alerts Issued: | Subject | No. of Alerts | Aircraft or aircraft equipment | 11 | Airport facility or procedure | 8 | ATC equipment or procedure | 7 | Company policies | 2 | TOTAL | 28 | Special Studies In cooperation with the FAA, ASRS is conducting an ongoing study on wake vortex incidents, enroute and terminal, that occurred within the United States. Learn more » ASRS, in cooperation with the FAA, is gathering reports of incidents that occurred while pilots were utilizing weather or AIS information in the cockpit obtained via data link on the ground or in the air. Learn more » |